Digital alter ego: what it means, its types, and technology
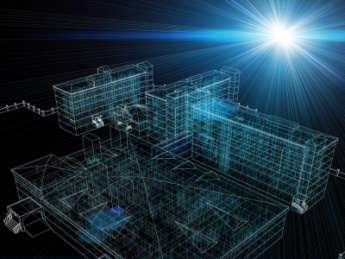
Business was always eager to work out all risks in advance and make its product as profitable as possible. This is the case with both digital technologies and production processes.
• Faster testing;
• Better analytics;
• Lower costs of functional testing under various conditions.
The technology is rapidly developing and is implemented at many enterprises every year.
What is a digital alter ego?
Initially, the technology was developed for space exploration programs to calculate loads on shuttles and satellites beyond the Earth’s atmosphere. The benefits of this approach for ground devices soon became evident, and the system was adapted for specific products or entire enterprises. Briefly, a digital alter ego is a virtual model of an object existing in real world. Transmitters are used to transfer real parameters of an object to the server and process those by means of specialized software, while potential situations are calculated by the IT infrastructure.The history
The idea of digitizing production processes is not new and appeared soon after science-fiction ideas about virtual reality. However, before mid-2010s it was impossible to digitize processes and enterprises for operational tasks because of the technical limitations of computer systems.As soon as virtual reality and the internet of things (IoT) came into existence, digitizing went at full speed. It began from manufacturers whose products are subject to permanent loading, such as in aircraft and turbine industry and in machine building. Soon the merits of digital twins were appreciated by the mining, oil&gas, and metallurgical industries. By 2021, the efficiency of the technology was recognized by service companies and small-scale enterprises.
Why do we need the digital alter ago technology?
As the digital alter ago technology creates a complete copy of a real object through computer simulation, it is a preferred way for simulating various situations. Then, the results are analyzed and measures are taken, like in the following example:• A new motorcar engine is being designed;
• Its digital copy is created in a virtual environment;
• The virtual prototype mirrors the real thing up to the molecular level;
• Operational parameters are set in the virtual environment, from overload to using various types of fuel;
• Due to the mathematical precision of situation simulation, the virtual engine is damaged in the same way as its real-world twin.
Thus, the manufacturer gets data on the product vulnerabilities and can fix them promptly. For example, in the case of an engine, it may happen that the valves burn through at 40,000 km because of, say, a defective material or an engineer’s mistake. In reality, such a situation can result in unfavorable comments about the brand, lawsuits from the buyers, and billions of losses for the engine manufacturer.
However, the burnout of valves after a short mileage is detected in the virtual environment, and perhaps the engine is not yet on sale but is still being designed. Simulation allows a weak spot to be identified, and engineers can eliminate it before production starts. As a result, the company saves money, time, and protects its reputation.
Digital twins can be used in all industries, and a motorcar engine is just an illustrative example. A great advantage of digitization is that any situation can be simulated.
Classification digital twin types
There are many definitions as to what a digital twin is and there are as many types, starting from a “shadow” or a prototype to a specimen: the difference is in nuances of design and setup. However, the basic classification that enterprises use includes just three types.Informational digital twins: these are connected to real equipment and receive its status and information about the processes. In online mode, they either send the data to an operator or independently track, assess, and record any malfunctions. They are needed to diagnose the status of the object, for example, an intelligent production machine or an oilrig.
Predictive twins: they are capable of simulating actual operating conditions and predict object behavior in different situations. This type is useful for designing new goods, upgrading existing ones, and predicting the efficiency of processes under certain circumstances.
Operational digital twins: these simulate a company’s virtual work, streamlining the team’s synergy, transparency, and business efficiency. Among them, there are virtual offices (like Bitrix24) and comprehensive software (a Microsoft software package).
Constructing a digital alter ago is an expensive process that demands integration of a modern IT infrastructure and security protocols, purchase of computing capacities, and regular system upgrading. Nevertheless, the costs are fully repaid within a few months due to a general quality upsweep, timely maintenance of production facilities, and optimization of power consumption and work resources.
The diversity of digital twins
Virtual systems can also be classified according to the following digitized objects:• Products. Goods are virtualized when their durability or efficiency are to be simulated. Any product types can be analyzed.
• Processes. These are mainly production processes, and their digitizing can show the equipment wear rate or consumed power.
• Systems, for example, a digital twin of a stand-alone system, like a workshop or an oil well. It only controls a limited number of a company’s fields of activity.
• Enterprises. Such twins are integrated into the digital structure of a company and interact with the company as a whole, lubricating internal communication and forecasting profits.
Each type of the digital alter ego can be of use in its own way for companies of different levels. Generally, such a system can be regarded as efficient in any form.
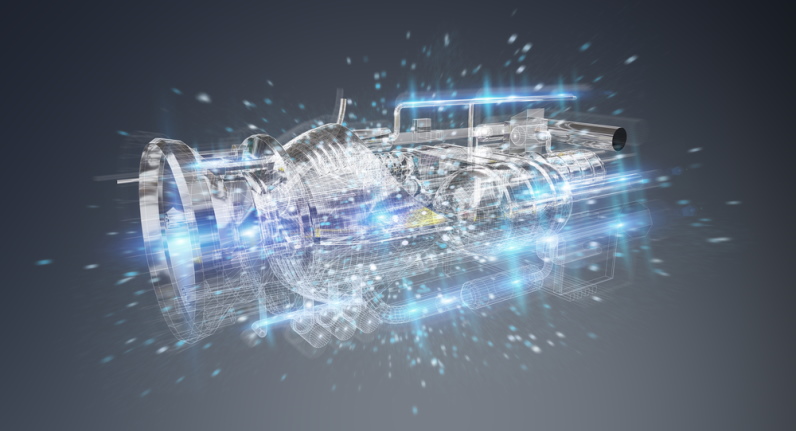
Beneficial effects resulting from implementation of a digital alter ago
The benefits of using virtual models with characteristics of a real object are evident:• Production risk assessment. Before entering production, a product can be tested and the market demand can be forecasted. However, the most important is the opportunity to prevent the production of defective items. The intensity of testing is increased many-fold, and engineers have an opportunity to test the product under most exotic conditions.
• Shorter design. Moreover, labor resources can be saved as well. The project creation and the adjustment periods become much shorter, thus making it possible to cut down salaries, reduce the staff, eliminate the human factor, and enter production as fast as possible.
• Timely maintenance. Digital twins calculate the degree of wear beforehand, indicate critical operational timeframes, enabling maintenance before the equipment is out of order. It saves money on repair and extends equipment life.
• Remote access to equipment. Digital twins enable equipment monitoring on a real time basis. It is not just diagnostics; it is also possible to interact with the equipment, for example switch it to a different mode. The technology is used for automated equipment and units in hard-to-reach destinations, including oil and gas wells.
• Teamwork. Office twins are designed to improve and speed up contacts in work teams. When such a system is used, executives spend less time for monitoring task execution, while staff members have around-the-clock access to a shared database and information exchange with other process participants.
• Optimized decision-making. Virtual simulation helps calculate the cost of processes and produce and assess financial risks in introducing new technologies, for example, an assembly line or conveyor belt. Without a digital model, the entire operation of a company has to be paused to test the new equipment, which can still fail to generate profit. Virtualizing allows making a decision on the necessity to upgrade technical processes before the actual equipment purchase.
A grave drawback is the sophisticated structure of digital twins, which entails high costs of the system implementation and maintenance. On the other hand, a virtual model yields a much bigger indirect profit and compensates for the integrational costs quickly.
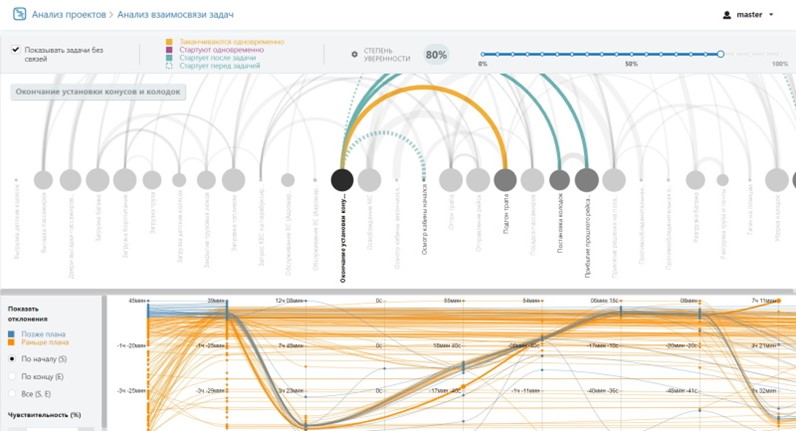
Where can digital twins be used?
A digital alter ego can find its place amongst all human activities. The most popular domains are industry and production. Digital twins calculate costs, equipment wear, output, and even power consumption. Nowadays, digital twins can be found:• In the extraction of mineral resources;
• In the processing industry that is in a common working chain with the mining industry
• In the production of cars, aircraft, space satellites, machines, military equipment and general goods;
• In public services where they calculate the load on a city’s life support systems in situations of extreme gravity or urgency;
• In construction, where they obtain data on solidity and stability of structures under the impact of different factors;
• In organizing the teamwork of a company’s staff and making it more efficient.
Digital twins have already proved themselves in business. Their benefits are apparent, that is why more companies are employing digital twins for their processes.